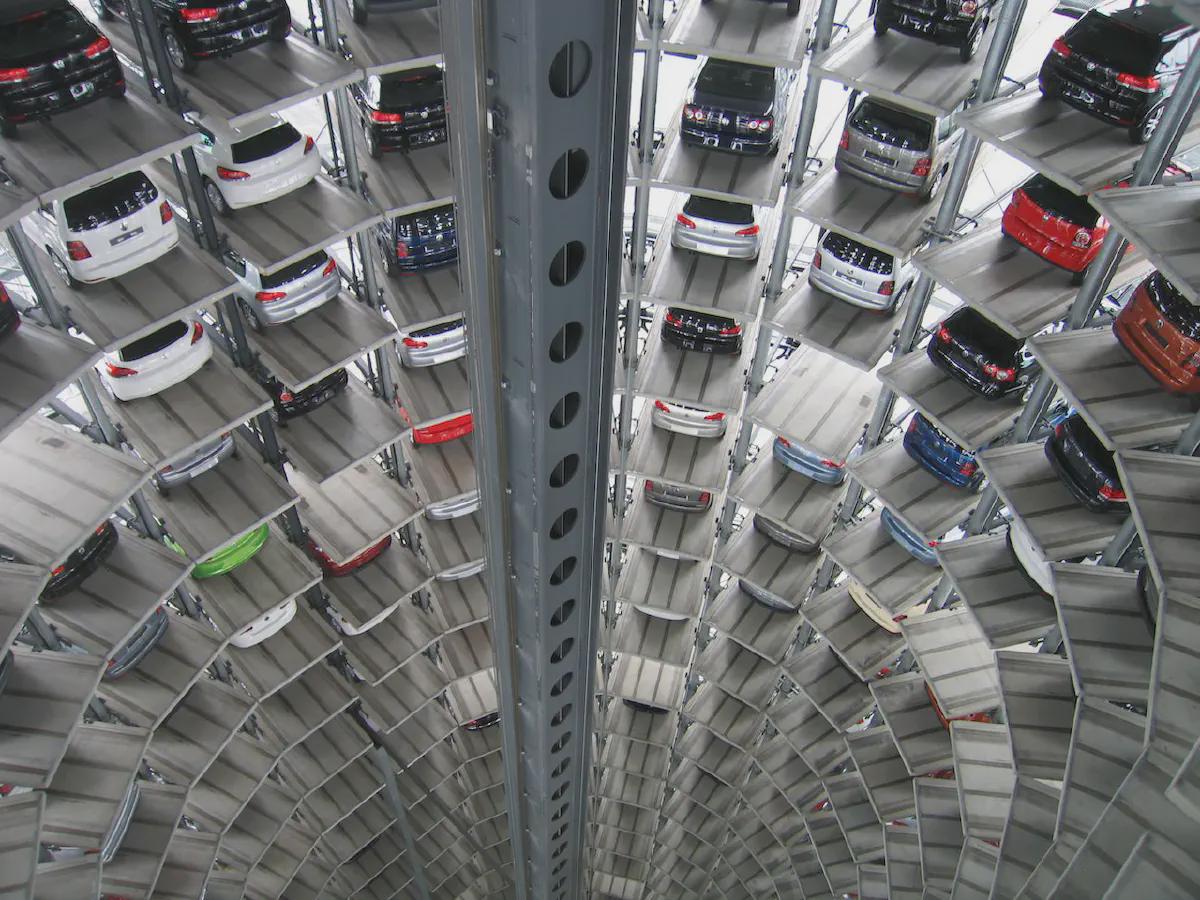
For companies in the highly competitive and complex automotive manufacturing industry, effective management of the supply chain is one of the key drivers of success. Automotive manufacturers must be capable of consistently delivering high-quality, low-cost products at a rapid clip, and for this to happen, all of the parts of their supply chain – just like the components of a car engine – must function efficiently as individual units and collaboratively as a whole.
Unfortunately, for many of these manufacturers, there is often a lack of visibility, control, and coordination across their operations, leading to planning and production problems, especially in the face of unexpected changes in customer demand or market conditions. These issues can even plague established operators, like Ford Otosan – an automotive manufacturing firm based in Turkey – which has a history stretching back all the way to 1959, when Otosan first began producing Ford automobiles. Ford Otosan, which was formed in 1977 as a joint venture between Ford and the Koc Group, currently employs over 10,600 workers and produces and exports a wide range of Ford automobiles as well as truck and commercial vehicles.
Challenges
Even though Ford Otosan successfully operates one of the most robust automotive manufacturing and distribution networks in Europe, the industrial powerhouse is not immune to thorny planning problems and corresponding production difficulties.
Ford Otosan’s Die Shop – which primarily handles contract-based projects that require extensive, initial data definition – was experiencing a multi-faceted planning predicament, leading to under-utilization of resources, higher costs, and sub-optimal performance.
The roots of the problem were:
- The planning department was utilizing project management software that was, in essence, a finite capacity scheduler and was not capable of generating plans that were feasible, flexible, and functional at the operational level.
- Planners were struggling to cope with the overwhelming amount of real-time, raw data coming from the shop floor on a daily basis, which had to be manually entered into the system so that production schedules could be revised – a cumbersome and time-consuming process.
- There was a need for a fully-automated decision support system at the contracting phase of projects to provide optimal timelines, resource requirements and estimated costs based on the current load state of the facility.
Ford Otosan’s Senior Manager of Tool & Die, Burak Gürler “The implementation of ICRON’s Optimized Decision Making solution has enabled Ford Otosan Die Shop to achieve some significant business benefits including increased speed, flexibility, and efficiency, cost reductions, resource optimization, and real-time visibility and control over our operations.”
Solution & Results
To solve Ford Otosan Shop’s planning challenges, ICRON implemented a two-pronged solution. The first element is ICRON’s Optimized Decision Making Solution, which provides highly configurable optimization capabilities for production planning and decision-making, enabling efficient day-to-day tactical planning as well as long-term, rough-cut capacity scheduling with extensive visual functionality and technical flexibility. The second element of the implementation is an execution system that manages front-end data collection. This custom-built execution system constantly feeds real-time data from the Die Shop floor to ICRON’s Optimized Decision Making platform, which in turn automatically revises production plans based on changes in project timeframes, customer priorities, material and resource usage, disruptions, and costs.
ICRON’s solution has revolutionized Ford Otosan’s Die Shop operations, resulting in numerous benefits including:
- An algorithm-based Optimized Decision Making system that empowers Ford Otosan’s planning team to process and analyze large amounts of project and production data on an ongoing basis, and enables them to rapidly and readily generate the most efficient schedules at any stage of the manufacturing process.
- Sophisticated analysis and reporting tools – such as used and planned resource reports and project-based and aggregate Gantt charts – that offer superior visibility across the project and resource space, produce detailed “what-if” scenario analysis, and enable easy identification of production bottlenecks before they become apparent.
- Enhanced resource utilization, reduced costs, and increased productivity and profitability.
- Ford Otosan Die Shop has experienced an overall operational process improvement of 25%
- Complete visibility and control over the entire manufacturing process and shop floor operations at the facility at all times.
- Fully automated generation of optimal plans and schedules, without any human intervention.
Ford Otosan’s Senior Manager of Tool & Die, Burak Gürler commented: “The implementation of ICRON’s Optimized Decision Making solution has enabled Ford Otosan Die Shop to achieve some significant business benefits including increased speed, flexibility, and efficiency, cost reductions, resource optimization, and real-time visibility and control over our operations.