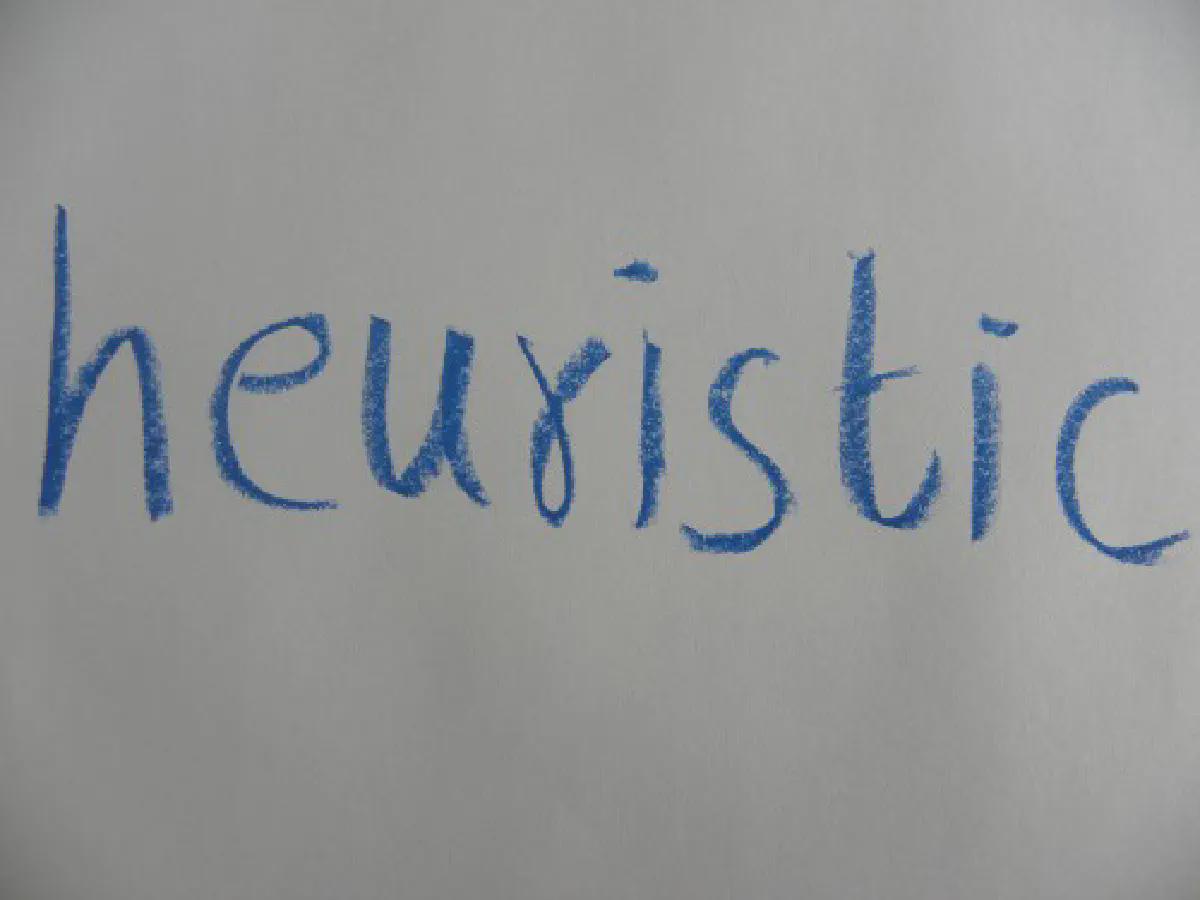
In today’s hypercompetitive and highly complex business environment, companies are constantly searching for ways to gain a competitive advantage by improving the speed, efficiency, and quality of the goods and services they deliver to customers through their supply chains. The key to unlocking success in supply chain management is being able to make optimized business decisions by finding the best possible solution to your company’s planning and scheduling problems.
There are many techniques – such as constraint programming, mathematical programming, metaheuristics, local search, machine learning algorithms and evolutionary algorithms like genetic algorithms and simulated annealing – that are used to solve supply chain planning and scheduling problems. These algorithms can be classified into two main categories: heuristics and optimization.
The aim of optimization and heuristic solutions is the same – to provide the best possible solution to a given supply chain problem – but their outcomes are often dramatically different.
Let’s examine the differences between optimization and heuristics and explore the pros and cons of each approach.
Defining the difference between heuristics and optimization
Fundamentally, every supply chain planning and scheduling problem is at heart an optimization problem. Its solution involves determining the best way to synchronize supply and demand across the supply chain network – to boost customer satisfaction and bottom-line results.
One popular technique that businesses employ to solve their supply chain planning and scheduling problems is heuristics. Simply put, a heuristic is a problem-solving approach that utilizes a practical process (commonly referred to as “rule of thumb” or “best practice”) to produce a feasible solution that is good enough to quickly solve a particular problem and achieve immediate goals – but not necessarily an optimal solution.
In contrast, an optimization model employs an intelligent, automated process to generate an optimal solution to a particular problem – taking decision variables such as production, inventory, and shipment quantities as well as constraints and key performance indicators (KPIs) into account. Supply chain optimization solutions aim to offer the best possible avenue to achieve optimal performance across your procurement, production, inventory, and distribution operations – maximizing delivery performance and overall profitability.
The pros and cons of the heuristic approach
The main advantage of adopting a heuristic approach is that it offers a quick solution, which is easy to understand and implement. Heuristic algorithms are practical, serving as fast and feasible short-term solutions to planning and scheduling problems.
The main downside of the heuristic approach is that it is – in the vast majority of cases – unable to deliver an optimal solution to a planning and scheduling problem.
Heuristic approaches can offer a quick fix to a specific planning or scheduling issue, but are not capable of serving as viable solutions that deliver the best possible results. This means that heuristics tend to “leave money on the table” – they often stop with a solution, even though there are better solutions of the same problem that yield lower supply chain cost, higher order satisfaction performance or higher overall profit. Over time, as your business model and processes evolve and develop, heuristic solutions will inevitably falter and fail – as they are simply not supple enough to accommodate your company’s evolving needs and requirements.
Another disadvantage is the lack of flexibility that heuristic approaches possess. If, for example, key decision variables, constraints or KPIs change, or if a new machine is added to the production line that shifts the bottleneck in the production process, a hard- or pre-coded heuristic may no longer be capable of serving as a valid and viable solution and might need to be reconfigured. Furthermore, a modest change in your operational processes or the underlying data patterns, such as distribution of demand over time or product mix, can have a major impact on the performance of the heuristic – and this can pose a serious risk to your company’s overall productivity and profitability.
In sum, heuristic techniques are practical and offer fast and feasible short-term solutions to planning and scheduling challenges, but lack the power and flexibility to create ongoing, optimal solutions that create pathways to greater productivity and profitability.
The pros and cons of the optimization approach
The main advantage of the optimization approach is that it produces the best possible solution to a given planning and scheduling problem.
Indeed, optimization algorithms are guaranteed to generate optimal solutions, which outperform their heuristic counterparts and enable businesses to maximize cost- and operational-efficiency.
One of the chief benefits of optimization models is their flexibility, as they can automatically adjust and adapt to consider the myriad decision variables and changing goals, constraints, and complexities in any business environment and generate the best possible planning and scheduling solutions.
Optimization techniques empower planners to make optimized decisions and achieve higher levels of productivity and performance.
There are, though, some disadvantages to the optimization approach. Firstly, optimization models are highly sophisticated, and specific expertise and technologies are required to devise and deploy optimization solutions. For example, in order to generate an optimization solution, a thorough understanding of mathematical programming concepts and utilization of special solvers are necessary.
Also, compared to their heuristic counterparts, optimization algorithms typically take more time to execute – as they are mathematically difficult to solve. Furthermore, some real-world processes cannot be adequately modelled using linear optimization techniques, and it is sometimes difficult to model intangible business objectives such as “fairness” in an optimization model.
Which approach is right for your business?
Ultimately, there is no “best” approach to solving your supply chain planning and scheduling problems – it all boils down to which approach is right for your business. You need to elaborate on company priorities and capabilities to decide on the approach and tools you should choose.
If heuristic and optimization algorithms are compared in terms of solution quality, the latter is the clear winner. Solution quality is often a critical success factor for tactical and strategic level supply chain optimization decisions, which makes optimization a natural choice.
But if your business needs a reasonably good solution in a short amount of time, which is often the case in real-time operational settings, then a heuristic solution may be the right choice for you.
In many cases, however, a complementary approach between optimization and heuristics is the most effective solution. ICRON supports not only optimization and heuristics, but also other algorithmic paradigms including evolutionary algorithms, rule-based algorithms, local search and multi-objective optimization. And using ICRON’s innovative modelling system GSAMS, it is possible to design hybrid solution approaches.
For example, it is possible to employ a heuristic that utilizes business know-how and decision maker experience to generate a good solution for the problem. This heuristic solution can then be passed as a starting point to the optimization model. Then the solver either proves optimality or improves the heuristic solution instead of solving the problem from scratch.
Another hybrid solution approach that balances solution quality and computation time for those businesses that are urgently looking to solve a planning and scheduling issue, but don’t have time to wait for an optimal solution to be found is “optimization-based heuristics.” This type of heuristics employs optimization techniques to speed up the solution process and deliver solutions that are better than those generated by traditional heuristic approaches, but not necessarily optimal.
If you would like to see ICRON in action, please contact us. If you have enjoyed this blog, you can find more content that you might enjoy here.