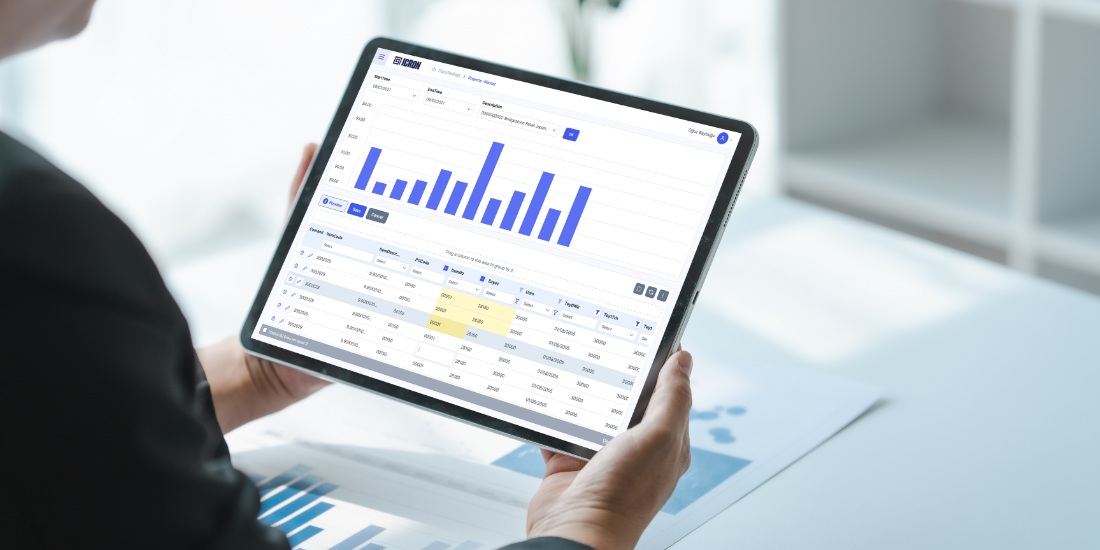
Multi-echelon inventory planning is a strategy for optimizing inventory management within global supply chains.
In this article, we’ll take a look at multi-echelon inventory planning and why has it become indispensable for supply chain management. We’ll also touch on how ICRON can help you along the way.
Understanding Multi-Echelon Inventory Planning
Multi-echelon inventory planning is a strategic approach to managing inventory across multiple levels – or “echelons” – of a supply chain network.
Traditional inventory management methods optimize each location independently, but multi-echelon planning considers the entire supply chain as a single, interconnected system, where inventory decisions at one level directly impact all others.
An “echelon” refers to any stage in the supply chain where inventory is held, from raw material suppliers and manufacturers to distribution centers, warehouses, and retail locations.
Multi-echelon inventory planning helps companies optimize inventory levels at each of these stages to minimize total costs while maintaining desired service levels. All told – and with a well implemented multi-echelon inventory planning strategy – companies can expect to reduce inventory by up to 30% while improving stock availability by up to 5%. [1]
The Importance of Multi-Echelon Inventory Planning in Modern Supply Chains
Multi-echelon inventory planning is fast becoming a mandatory endeavor, especially as supply chains grow in scope and sophistication.
Addressing the Complexity of Contemporary Supply Chains
Today’s supply chains are considerably more complex than those of previous decades. Globalization is a main factor here, with modern supply chains typically involving:
- Multiple suppliers across different geographic regions
- Several manufacturing facilities specializing in different products or components
- Numerous distribution centers and warehouses strategically positioned for market coverage
- Omnichannel retail including physical stores, e-commerce platforms, and direct-to-consumer options
Multi-echelon inventory planning accounts for all of these factors by optimizing inventory decisions across the entire network rather than treating each location as an isolated entity.
Key Components of Multi-Echelon Inventory Planning
A multi-echelon inventory planning strategy hinges on several interconnected parts. We’ll take a look at them here.
Integrated Inventory Management Across Echelons
Multi-echelon inventory planning requires organizations to integrate inventory management policies across all supply chain levels. This means they must develop a holistic view of inventory throughout the network, as well as make decisions that consider upstream and downstream implications.
The result is “inventory pooling effect” [2] that results in:
- Reduced impact from variations in demand across locations
- Reduced need for “safety stock”
- Reduced risk of stockouts
Advanced Demand Forecasting Techniques
Accurate demand forecasting at multiple points in the supply chain is foundational for effective multi-echelon inventory planning.
Companies that make use of advanced forecasting techniques across multiple echelons can expect to reduce inventory by as much as 25% [3] – an improvement that stems from better ability to distinguish between dependent and independent demand in different echelons.
Collaborative Planning and Coordination
Successful multi-echelon inventory planning requires close collaboration among various stakeholders across the supply chain. This collaboration includes:
- Sharing demand information
- Coordinating replenishment schedules
- Jointly planning for unexpected or seasonal demand spikes
Benefits of Implementing Multi-Echelon Inventory Planning
Multi-echelon inventory planning unsurprisingly brings a variety of benefits to organizations. Here are some of the most important.
Enhanced Cost Efficiency
By optimizing inventory levels across the entire supply chain, organizations can substantially reduce carrying costs while minimizing stockouts and expedited shipping expenses.
On average, companies implementing multi-echelon inventory optimization can hold 20% less inventory [4] while still maintaining adequate availability levels. For a company with $100 million in inventory, this translates to $20 million in freed-up working capital.
Improved Customer Service Levels
Beyond cost savings, multi-echelon inventory planning directly improves customer satisfaction by ensuring product availability.
By coordinating inventory across multiple levels like factories, central warehouses, regional hubs, and retail locations, companies can:
- Position products closer to where demand happens, so deliveries are faster
- Balance stock levels across the network, meaning if one location runs low, another nearby can cover the gap
- Use better demand forecasting, leading to fewer surprises and fewer stockouts
- Hold safety stock more intelligently, so there’s less risk of running out without overstocking
Such an improvement in service reliability usually translates to higher customer retention and increased sales.
Increased Supply Chain Agility
Multi-echelon inventory planning enhances supply chain agility by providing a more responsive and flexible approach to inventory management.
With better visibility and control over inventory at multiple points across the supply chain, you can:
- React faster to demand changes by shifting inventory between locations instead of waiting for new production
- Adapt to disruptions like supplier delays or transport issues because you have backup stock at different levels
- Optimize inventory flow dynamically, based on real-time conditions
- Prioritize critical products or regions quickly when unexpected demand spikes occur
Challenges in Implementing Multi-Echelon Inventory Planning
Multi-echelon inventory planning is undeniably advantages, but it also presents significant challenges due to its complexity and scope.
Data Integration and Accuracy
Effective multi-echelon inventory planning requires comprehensive and accurate data from multiple sources across the supply chain. Integrating separate data sources while ensuring data quality is a significant challenge for many organizations.
Common issues include:
- Inconsistent data formats
- Varying time horizons
- Differing metrics across supply chain partners
Complexity in Coordination
Coordinating inventory decisions across multiple echelons involves aligning different stakeholders’ objectives and constraints, each of which often have their own priorities and performance metrics.
Without effective methods of coordination and collaboration, even the most sophisticated inventory optimization models will deliver suboptimal results.
Technological Requirements
Implementing multi-echelon inventory planning typically requires advanced supply chain management solutions capable of handling complex optimization algorithms and processing large volumes of data in real-time.
While this investment can deliver significant returns, it usually represents a substantial commitment of both financial and organizational resources.
Best Practices for Successful Multi-Echelon Inventory Planning
We’ve noticed organizations that successfully leverage multi-echelon inventory planning typically follow these strategies.
Investing in Integrated Supply Chain Technologies
Perhaps obviously, technology is an essential enabler of multi-echelon inventory planning. Modern supply chain solutions provide the visibility, analytics, and optimization capabilities that are necessary to make informed inventory decisions across complex networks.
Key technological capabilities for multi-echelon inventory planning include:
- Network-wide inventory visibility
- Advanced demand forecasting
- Inventory optimization algorithms that consider multiple echelons simultaneously [5]
- What-if scenario modeling
- Real-time analytics and performance monitoring
Establishing Collaborative Relationships with Supply Chain Partners
Successful multi-echelon inventory planning by nature requires collaboration with suppliers, distributors, and other supply chain partners.
Companies with optimized collaborative planning processes are typically able to better forecast plan, forecast, and replenish inventory. [6] In the context of multi-echelon inventory planning, collaboration usually involves:
- Regular information sharing
- Joint planning processes
- Aligned performance metrics
Continuous Monitoring and Optimization
Multi-echelon inventory planning is not a one-time implementation. Instead, it is an ongoing process of monitoring, analysis, and refinement. Leading organizations establish regular review processes to evaluate inventory performance and adjust strategies as demand shifts, for example.
This approach to continuous improvement helps ensure that inventory strategies remain aligned with business objectives and market conditions.
Case Studies: Successful Implementation of Multi-Echelon Inventory Planning
Procter & Gamble’s Integrated Supply Chain
Procter & Gamble (P&G), one of the world’s largest consumer goods companies, is a pioneer in multi-echelon inventory planning.
About 30% of its business units now use it, with plans to grow to over 65% in three years. This shift from single-stage to full inventory management across supply chain stages also dramatically cut inventory costs across the company’s supply chain, saving $1.5 billion in 2009 alone. [7]
Caterpillar’s Global Parts Distribution Network
Caterpillar, a leading manufacturer of construction equipment, implemented multi-echelon inventory planning to optimize its global service parts network.
This includes manufacturing facilities, regional distribution centers, dealer locations, and customer sites – a deeply rooted network that allows the company to fill 98% of all customers’ orders for parts within 24 hours. [8]
Future Trends in Multi-Echelon Inventory Planning
As technologies like AI, blockchain, and advanced analytics continue to evolve, the capabilities and impact of multi-echelon inventory planning will only increase.
Organizations that invest in developing these capabilities now will be well-positioned to outperform competitors and deliver better value to customers for years to come. We’ll take a closer look at these trends in the following section.
Integration of Artificial Intelligence and Machine Learning
Artificial intelligence and machine learning hold revolutionary power for multi-echelon inventory planning by allowing more accurate forecasting, real-time optimization, and automated decision-making.
For example, AI-powered multi-echelon inventory optimization strategies result in optimized inventory levels by as much as 35%, as well as 65% faster service. [9] This is thanks to algorithms that can identify complex patterns and relationships that human planners or conventional statistical methods might miss.
Blockchain Technology for Enhanced Transparency
Blockchain technology can bolster supply chain inventory optimization because it provides extreme visibility and traceability across the entire network. [10] These benefits are particularly significant in industries with complex supplier networks and stringent traceability requirements, such as aviation or high tech.
Sustainability Considerations in Inventory Planning
Environmental, social, and governance (ESG) factors are increasingly being integrated into multi-echelon inventory planning as organizations recognize the sustainability impact of their inventory decisions.
By taking steps to optimize transportation routes, reduce waste from obsolescence, and right-size facilities, companies can reduce emissions and resource consumption – thus saving costs – while adhering to increased pressure for regulatory bodies and consumers alike.
Develop and implement a multi-echelon inventory planning strategy with ICRON
Ready to take control of inventory management across supply chain stages? ICRON’s advanced multi-echelon inventory planning capabilities help you optimize stock levels at every point – from suppliers to distribution centers to retail locations.
With AI-powered insights, real-time visibility, and predictive analytics, ICRON enables smarter inventory decisions that balance cost, service levels, and risk. Get in touch to learn more.
References
- https://www.sciencedirect.com/science/article/abs/pii/S0377221723006173
- https://www.researchgate.net/publication/227448016_On_the_Benefits_of_Inventory-Pooling_in_Production-Inventory_Systems
- https://www.numberanalytics.com/blog/7-demand-forecasting-techniques-retail-ecommerce
- https://supplychaindigital.com/supply-chain-risk-management/multi-echelon-future-competitive-supply-chains
- https://www.numberanalytics.com/blog/streamlining-modern-logistics-supply-chain-optimization
- https://www.researchgate.net/publication/241970086_Supply_chain_collaboration_for_improved_forecast_accuracy_of_promotional_sales
- https://www.researchgate.net/publication/220249734_Inventory_Optimization_at_Procter_Gamble_Achieving_Real_Benefits_Through_User_Adoption_of_Inventory_Tools
- https://www.cat.com/en_ZA/by-industry/electric-power/product-support/parts/ep-parts-distribution-centers.html
- https://www.mckinsey.com/industries/metals-and-mining/our-insights/succeeding-in-the-ai-supply-chain-revolution
- https://www2.deloitte.com/us/en/pages/operations/articles/blockchain-supply-chain-innovation.html