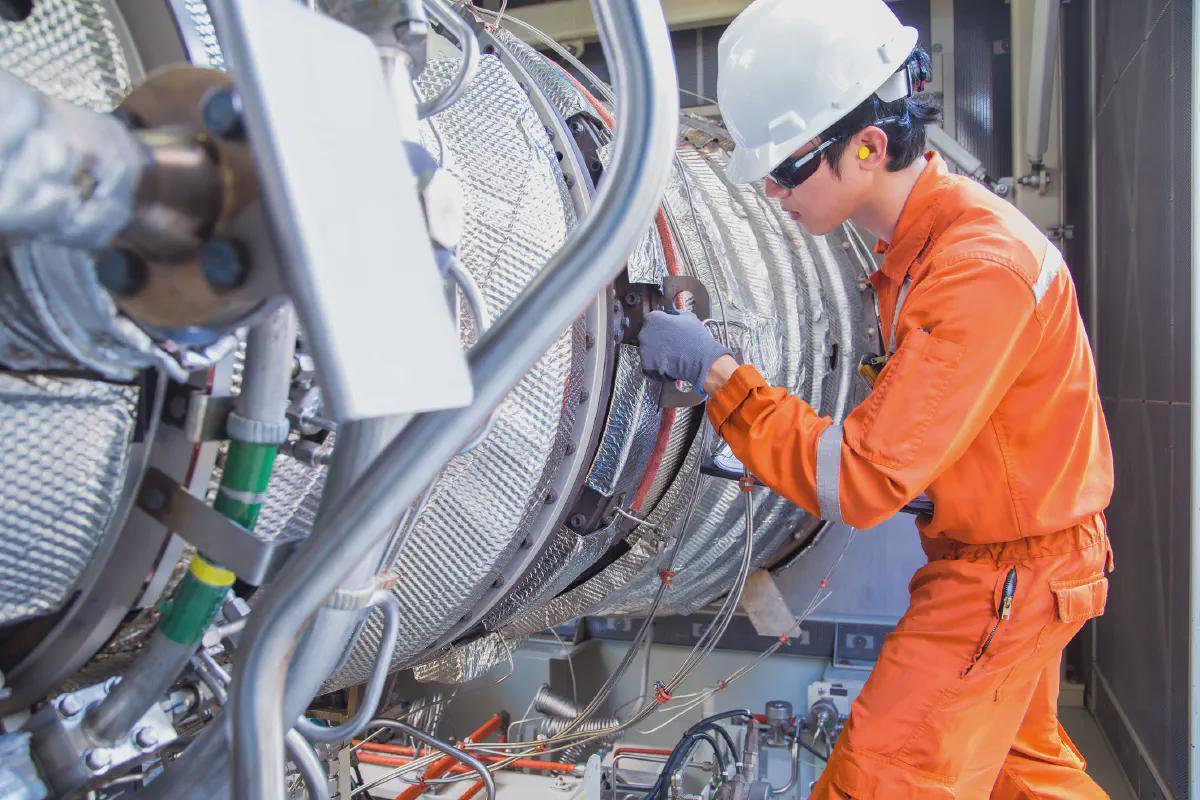
Authors: William Citrin from ICRON and Minou Olde Keizer from CQM
Supply chain executives around the world and across various industries – from manufacturing to mining to public transport to oil & gas to maintenance, repair, and overhaul (MRO) – are all abuzz about predictive maintenance.
A revolutionary, state-of-the-art maintenance strategy, predictive maintenance allows companies to continuously monitor and assess the condition of their assets (such as manufacturing machines, airplanes, trains, trucks, offshore oil drilling rigs, or cranes), predict precisely when these assets will need maintenance, and perform maintenance only when necessary – thus simultaneously slashing maintenance costs and asset downtime.
But what does your company actually need to perform predictive maintenance-based planning and operations?
Firstly, you need access to real-time and historical data on the performance of your company’s assets (so that you can gauge the condition of those assets on an ongoing basis) as well as the right intelligent planning and optimization technologies (to transform your data into optimized plans that identify the best window of time in which to schedule predictive maintenance activities).
Besides the current condition of the assets, these plans should also take into account the availability of the specific workers, equipment, and spare parts necessary to conduct predictive maintenance – and the last requirement, in particular, poses quite a significant challenge.
Highly specialized and extremely costly, spare parts are a tricky (but essential) part of the predictive maintenance planning puzzle.
When asked to identify the source of maintenance delays, many supply chain companies and MRO providers point to difficulties in obtaining spare parts from their suppliers. Indeed, spare parts unavailability is frequently the bottleneck that causes protracted asset downtimes and, ultimately, drops in service-level performance, customer satisfaction, and resource utilization as well as spikes in operating costs.
Spare parts are a small but crucial component of the maintenance process – without them predictive maintenance (or any type of maintenance at all, for that matter) is not possible.
The root of the spare parts problem
For supply chain companies and MRO providers, ensuring that the required spare parts are in the right places at the right times to conduct predictive maintenance presents a tremendous challenge.
The root of the problem is that, with predictive maintenance, maintenance activities are only scheduled when they are warranted based on the real-time condition of an asset (and not according to a prescribed maintenance plan) – and this makes it harder to foresee and anticipate demand for spare parts.
So, with predictive maintenance, it’s difficult to determine when and where and which spare parts will be needed. Add to this the fact that spare part manufacturers often have long lead times – and ordering them at the last minute will likely result in service delays.
You may wonder: why don’t companies just keep safety stock of spare parts at all their facilities? Because, typically, these components are very costly, and – as demand for them is sporadic and low – it only makes sense (from a financial perspective) to hold very limited stock of spare parts.
Thus, companies must try to maintain just the right amount of spare parts in the right places at the right times to keep spare parts inventory costs down and keep service levels high. How is this possible?
Solving the spare parts problem
At its core, this thorny spare parts problem is an inventory issue – and in order to solve it you need an intelligent planning and optimization system.
With such a system, your company can automatically generate spare parts inventory plans that optimally balance the tradeoff between service levels and costs, taking into account:
- The data on the past performance and current condition of your company’s assets that is collected and used to create predictive maintenance plans. This data, along with the maintenance plans themselves, can be utilized to help forecast demand for spare parts and formulate “predictive” spare parts inventory plans.
- Your entire customer network and the demand rate for spare parts among these businesses (which can be determined by utilizing probabilistic forecasting techniques).
- Service level agreements (SLAs) with individual customers, and spare part dependencies.
- The utilization and availability of the capacity (specialized workers and equipment) required to carry out maintenance activities.
With an intelligent planning and optimization system, your company can create data-driven, “predictive” spare parts inventory plans that are integrated with your predictive maintenance-based plans and operations.
Your company will be able to minimize spare parts inventory levels and costs (by only ordering the components when they are required) and minimize asset breakdowns and downtime (by ensuring that the right spare parts are available in the right locations at the right times to conduct predictive maintenance).
If you would like to see ICRON in action, please contact us. If you have enjoyed this blog, you can find more content that you might enjoy here.