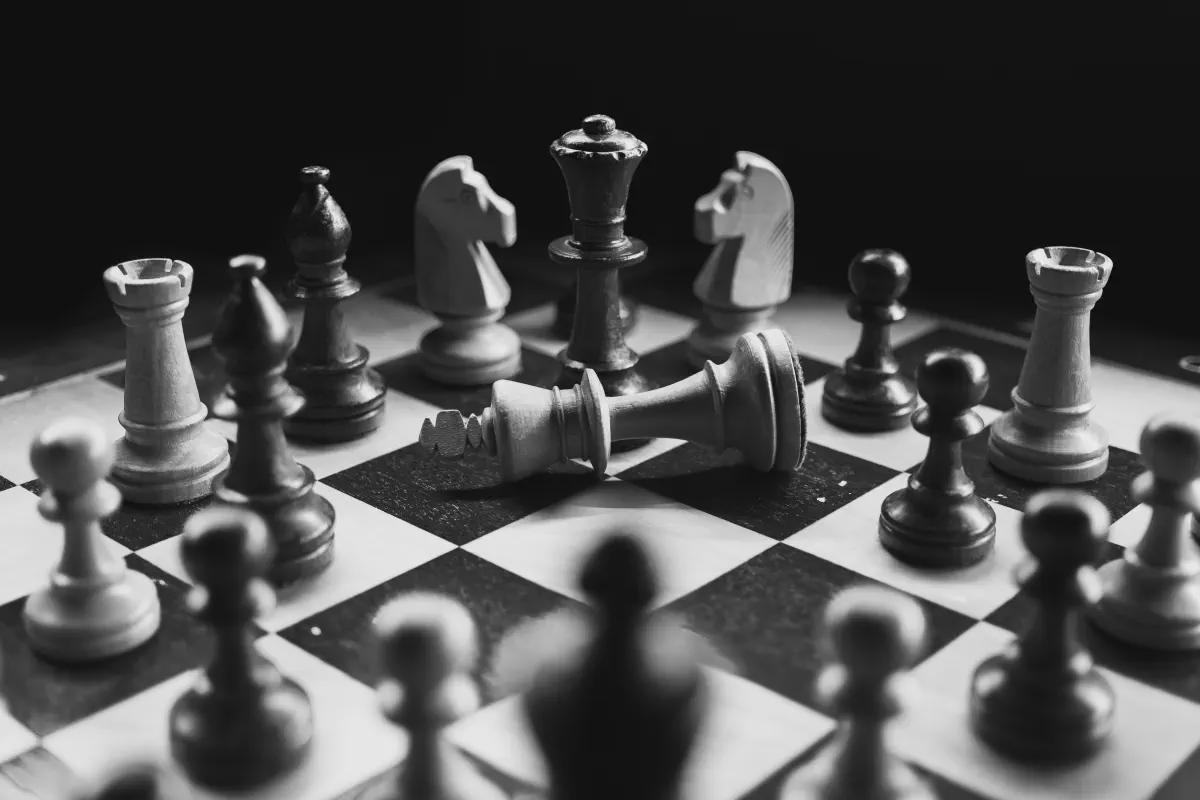
Author: Korhan Kılçar
Most industry professionals want to manage a deterministic world by eliminating the factors beyond their control as much as possible while managing their businesses. They aim to reduce the probability of being affected by the disruptions, in other words, their risk. Because managing a world where everything is under control and predictable is much easier than managing a world with uncertainties and disruptions.
In supply chain planning as well, it is almost impossible to isolate ourselves from out-of-control drivers due to the nature of the business. That is why it is crucial to at least know and measure risk factors in terms of risk management.
One of the clearest reflections of the issue on supply chain planning is the promises you make to your customers to deliver your orders on time and manage the risk of not fulfilling this commitment.
Even without realizing it, we take certain risks while fulfilling orders with limited resources. Working overtime, delaying the planned machine maintenance activities, or using the stock you keep for emergencies in order to fulfill your orders are all sources of risk. Moreover, these decisions are not only a risk for current orders but also for subsequent ones. Because the disruption may cause the order that you deterministically said “will be delivered on this date” not to go on that date, and it also interrupts the delivery plan of the upcoming orders.
In addition, if you consider material-related risks, using the safety stock you have reserved for urgent orders to fulfill the current order may cause a really urgent order not to be sent on time.
Measuring the significance of the risk is important, at the point you decide whether to take that risk or not.
Think about a situation where you fulfilled your order by delaying the maintenance of a machine for 2 weeks and by making this decision, one of your more important orders is delayed. At this point, you can consider not taking this risk by evaluating the significance of the risk and deciding to change the priority of the current order and send it later.
In this context, factors such as
- order status
- the importance of the customer for the company
- the breakdown frequency of the machine in which the product is made
- resupply time of stock used for the order
are important parameters for risk measurement. Measuring risk based on these parameters and making operational decisions accordingly is a prerequisite for successful order management.
Besides this, the risk you are willing to take can be shaped according to your company’s strategy. The tendency to take more orders is directly related to your risk appetite. At this point, the benefit you will get from the risk you take can be an important decision factor for you to evaluate and manage risks.
You can proactively manage your risks with ICRON’s end-to-end supply chain planning solution.
With ICRON, you can:
- prioritize your orders by evaluating the distribution of risk by orders over time
- postpone orders above a certain risk threshold or activate less risky production alternatives depending on the risk trend
- work with suppliers with shorter lead times or increase safety stock levels in order to reduce material risks
- turn to alternative machine sources in order to reduce machine risks
- compare how much each action you take affects the risk parameters with scenario analysis and prepare multiple alternative plans accordingly
If you would like to see ICRON in action, please contact us. If you have enjoyed this blog, you can find more content that you might enjoy here.