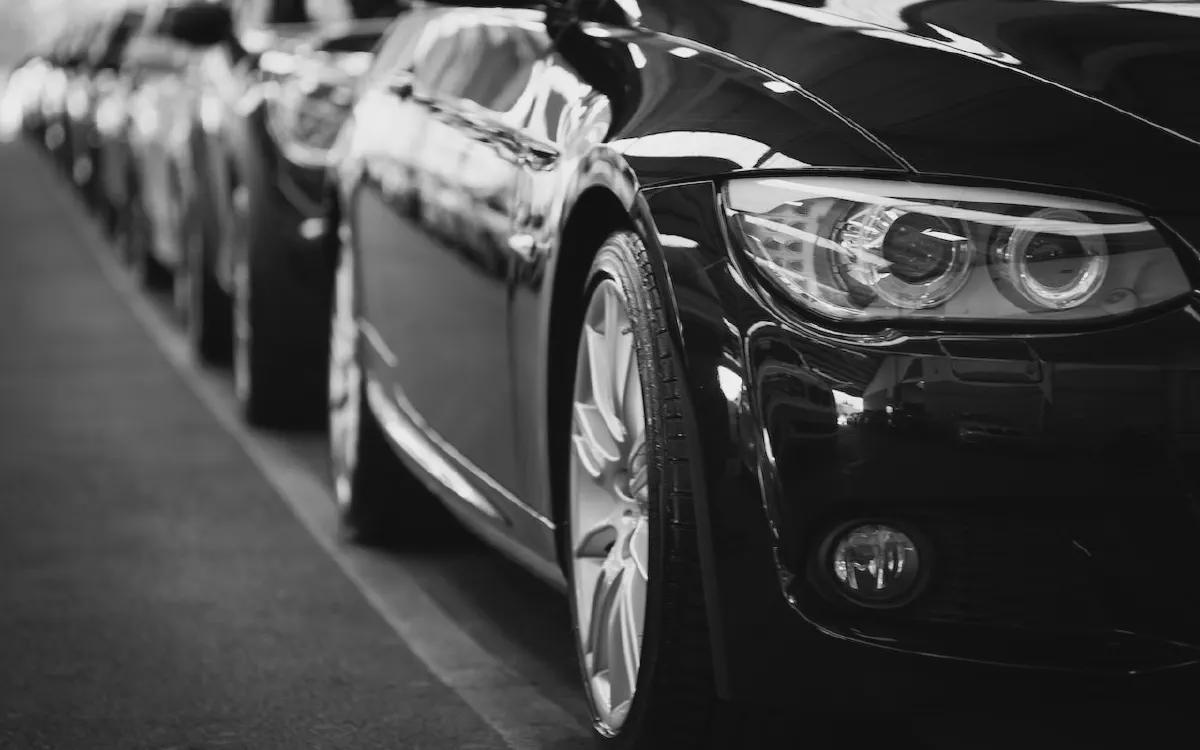
In the fast-paced, ultracompetitive automotive manufacturing industry, time is money as disruptions in production can lead to costly delays and dissatisfied customers. To ensure ongoing productivity and profitability, manufacturers must have the capability to create feasible schedules that take into account the complex and constantly changing reality of shop floor operations.
Even established operators like Ford Otosan – an automotive manufacturing giant based in Turkey that has been producing vehicles since 1959 and currently employs over 10,600 workers – can experience difficulties in synchronizing their planning and production operations. The planning department at Ford Otosan’s Press Shop – which functions as a standalone manufacturer, producing press panels for the cars and vans assembled in Ford Otosan’s factories – was struggling to generate viable schedules to keep its shop floor operations running smoothly and in sync with the rest of the supply chain.
Challenges
As one vital link in a high-speed and sophisticated supply chain network, Ford Otosan needed to put in place an automated system that would enable its Press Shop planners to continually devise and revise:
- Short-term schedules to handle the daily requirements of the assembly lines and spare part distribution system, minimize the set-up times of the progressive presses used to produce the press panels, optimize workforce and machinery utilization, and maximize output.
- Long-term plans to forecast future sheet metal and container needs and automatically create accurate steel requirement reports so that exact due dates and precise requirement quantities could be communicated to suppliers. Ford Otosan was utilizing a Computerized Material Management System (CMMS) to track data on its products, steel sheets and containers inventory, bill of materials, engineering changes, and daily and weekly press panel requirements. But this CMMS did not possess the capability to define the Press Shop’s production processes, collect real-time data from the shop floor, and offer planners the visibility and capacity to generate reliable production schedules based on changing conditions and constraints. Solution & Results Ford Otosan Press Shop’s planning and production operations were out of sync, and so the manufacturer looked to ICRON to implement a solution that would provide the optimization of decision making process and enable the planning and production teams to work in concert to achieve optimal operational efficiency and productivity.
ICRON’s Optimized Decision Making solution for Ford Otosan consisted of three parts:
- An advanced finite capacity scheduler and a rough-cut capacity planner, giving the Press Shop planning team the capability to oversee and control day-to-day, production scheduling and sequencing of press operations as well as long-term, rough-cut capacity planning by using the visual functionality and technical flexibility of ICRON’s GSAMS (Graphical Scheduling Algorithm Modeling System).
- An execution front-end, the ICRON Database Interface, which is integrated with Ford Otosan’s CMMS, allowing planners to monitor detailed data coming from the shop floor on a daily basis, modify and optimize production plans based on current constraints and fluctuations in supply and demand, and make “what-if” analysis by simply changing scheduling parameters.
- A data collection system that synchronizes daily shop floor operations with Ford Otosan’s CMMS and ICRON’s solution. With the implementation of ICRON’s Optimized Decision Making solution, Ford Otosan’s Press Shop now has in place a sophisticated shop floor management system through which the processes of preparing production schedules, communicating these schedules to staff on the shop floor, collecting production data, updating stock quantities and production parameters in the CMMS, and preparing short- and long-term sheet metal acquisition plans are all fully automated.
Ford Otosan’s planners now have the power to easily create adapted, optimized schedules that are compatible with real-world shop floor manufacturing processes, allowing them to maximize resource utilization, minimize set-up times and work-in-process inventory levels, and determine long-term steel requirements. With ICRON’s Optimized Decision Making system, Ford Otosan Press Shop’s planning and production operations have been synchronized, delivering significant cost- and time-savings and driving increased productivity and profitability. The efficiency improvement was estimated at 20 percent in the first year after go-live.