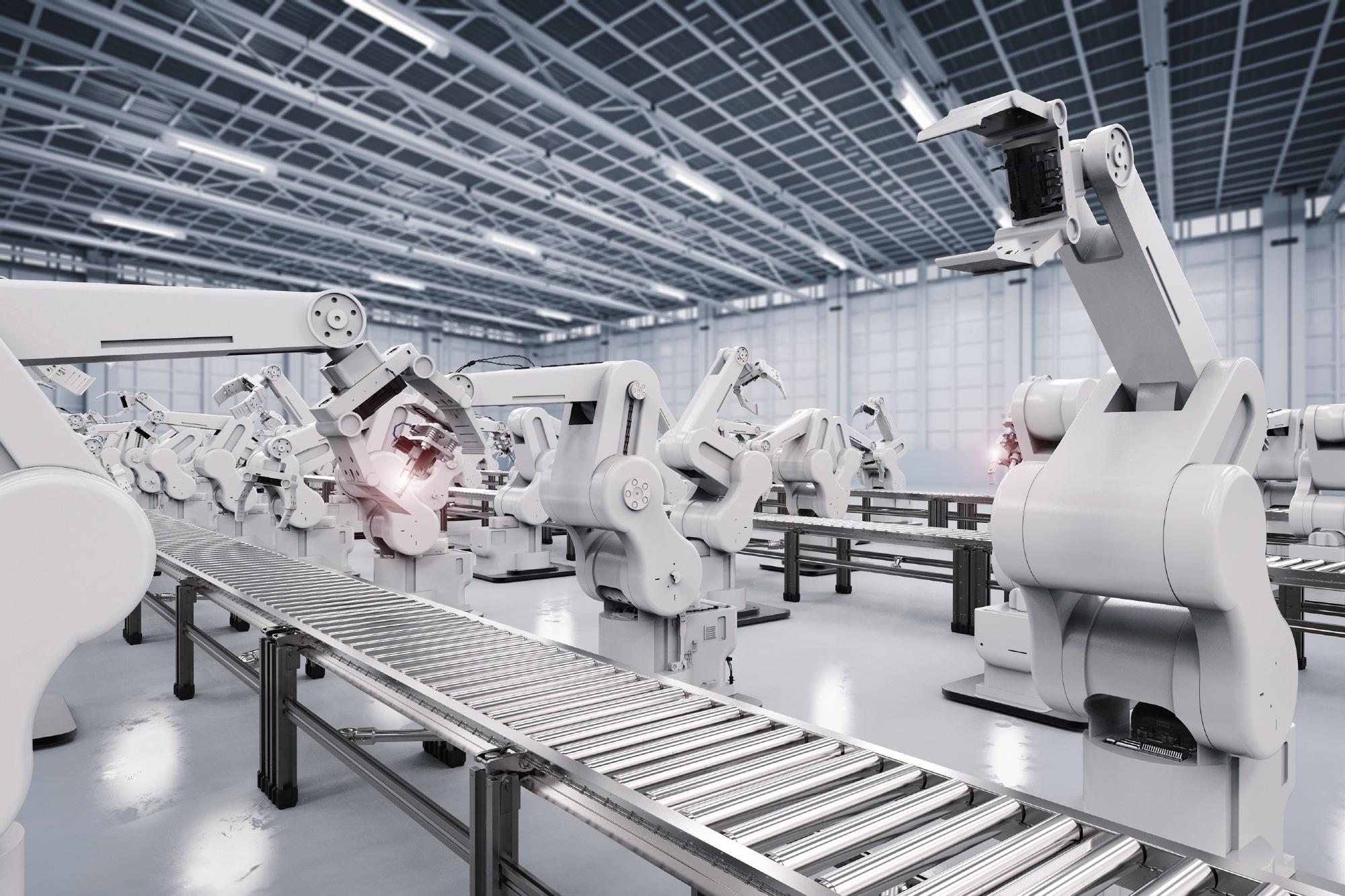
Authors: William Citrin from ICRON and Minou Olde Keizer from CQM
Predictive maintenance – a groundbreaking maintenance strategy that enables companies to continuously monitor and gauge the condition of their assets using real-time and historical data, accurately predict when these assets will require maintenance, and recommend the optimal time to schedule and perform maintenance activities – has become immensely popular.
This is particularly the case among companies in asset-intensive industries such as utilities, mining, shipping, public transport, and aviation – where assets such as airplanes, trains, trucks, and cranes form the backbone of their business. In these asset-intensive industries, preventing asset downtime and decreasing maintenance costs can provide a big boost to the bottom line.
A growing number of companies in the manufacturing industry, however, have also been discovering the power of predictive maintenance-based planning and operations. Indeed, more and more manufacturers are realizing that predictive maintenance of their production machines and equipment can yield significant business benefits – enabling them to prevent costly breakdowns and increase overall operational efficiency and production throughput.
Moving beyond the traditional approach
Traditionally, manufacturers have taken a two-pronged approach to conducting maintenance: preventive and corrective. With the former method, manufacturing companies perform a fixed sequence of maintenance activities according to a prescribed schedule – and thereby proactively prevent asset failures. With the latter strategy, manufacturers adopt a more reactive approach to maintenance through which they seek to respond to any asset malfunctions and breakdowns that have already occurred and repair them as rapidly as possible.
These traditional maintenance strategies typically lead to spikes in maintenance costs (for unnecessary preventive maintenance activities that are performed as a part of a preset schedule) and asset downtime (as corrective maintenance activities are only carried out after an actual breakdown and production disruption occurs).
But now, there is a better way: predictive maintenance. With the advent of Industry 4.0 technologies – such as IoT devices, data collection and storage systems, and advanced analytics, AI, and ML algorithms – manufacturing companies have access to a treasure trove of data and insights on the past performance and current condition of their assets.
Armed with all this information on their assets flowing from these new technologies as well as their ERP and MES systems, manufacturers are perfectly positioned to conduct predictive maintenance – which is scheduled and executed based on the present state (and predicted future performance) of their production machines and equipment.
Indeed, with the right intelligent planning and optimization tools to go along with their Industry 4.0 technologies, manufacturers can capitalize on all this real-time and historical data and analytics-driven insights and utilize them to craft predictive maintenance-based plans – that maximize the efficiency of their production assets and minimize maintenance times and costs.
Addressing manufacturing maintenance challenges
For manufacturing companies, predictive maintenance is a game-changing strategy, through which they can harness the power of their Industry 4.0 technologies to monitor the real-time health of their assets, foresee asset malfunctions and breakdowns before they happen, and formulate optimal maintenance schedules.
With predictive maintenance-based planning and operations, manufacturers can address and overcome some of the thorny, industry-specific maintenance challenges they face including:
- Avoiding production disruptions: Every manufacturer aims to keep their operations running non-stop – to mitigate production delays and disruptions and improve efficiency, throughout, and service-level performance. By predicting and preventing asset issues, predictive maintenance does exactly that.
Additionally, with predictive maintenance, manufacturing companies can generate maintenance schedules that are seamlessly integrated with their production plans and schedules – taking into account all of their customer orders as well as their equipment and workforce requirements, capacities, and constraints. This ensures that the maintenance activities will not impact their overall production flow, shift patterns, and delivery performance.
- Reducing set-up times and costs: One of the main challenges for manufacturers – especially those who operate in process manufacturing environments and produce goods like food, beverages, chemicals, and building materials according to a specific recipe or formula – is minimizing set-up times and costs. To achieve this, manufacturers try to schedule their operations to produce goods in large batches, thereby avoiding unnecessary set-ups.
With predictive maintenance-based planning, maintenance activities can be scheduled and carried out during the same period of time as set-up activities – thus dramatically minimizing overall asset downtime.
There are also set-up times and costs associated with maintenance activities – and, with predictive maintenance-based planning, these can be reduced by optimally grouping together various maintenance tasks that can be performed simultaneously.
- Availability of resources: Another critical issue that manufacturers must contend with is the limited availability of resources (specialized workers, equipment, and spare parts required to perform maintenance on their machines and components. These maintenance resources are often shared among various production lines or facilities.
With predictive maintenance-based planning, manufacturers can optimize the utilization of their maintenance resources – to make sure that the right personnel, equipment, and spare parts are available at the right places and right times.
Getting the most out of manufacturing assets
Manufacturers today, who operate in a highly complex and hotly competitive business landscape, must look for ways to carve out a competitive advantage – and predictive maintenance is one such way.
With predictive maintenance, manufacturing companies can utilize the data and insights delivered by their Industry 4.0 technologies to generate maintenance plans and schedules that:
- Optimize the timing and duration of their maintenance activities – based on the current condition and past performance of their assets.
- Are perfectly integrated with their production plans and schedules, and take into account all the variables, dependencies, and constraints of their unique manufacturing environment.
- Enable them to minimize asset downtimes and maintenance costs, and maximize asset utilization, production efficiency, and customer satisfaction.
If you would like to see ICRON in action, please contact us. If you have enjoyed this blog, you can find more content that you might enjoy here.