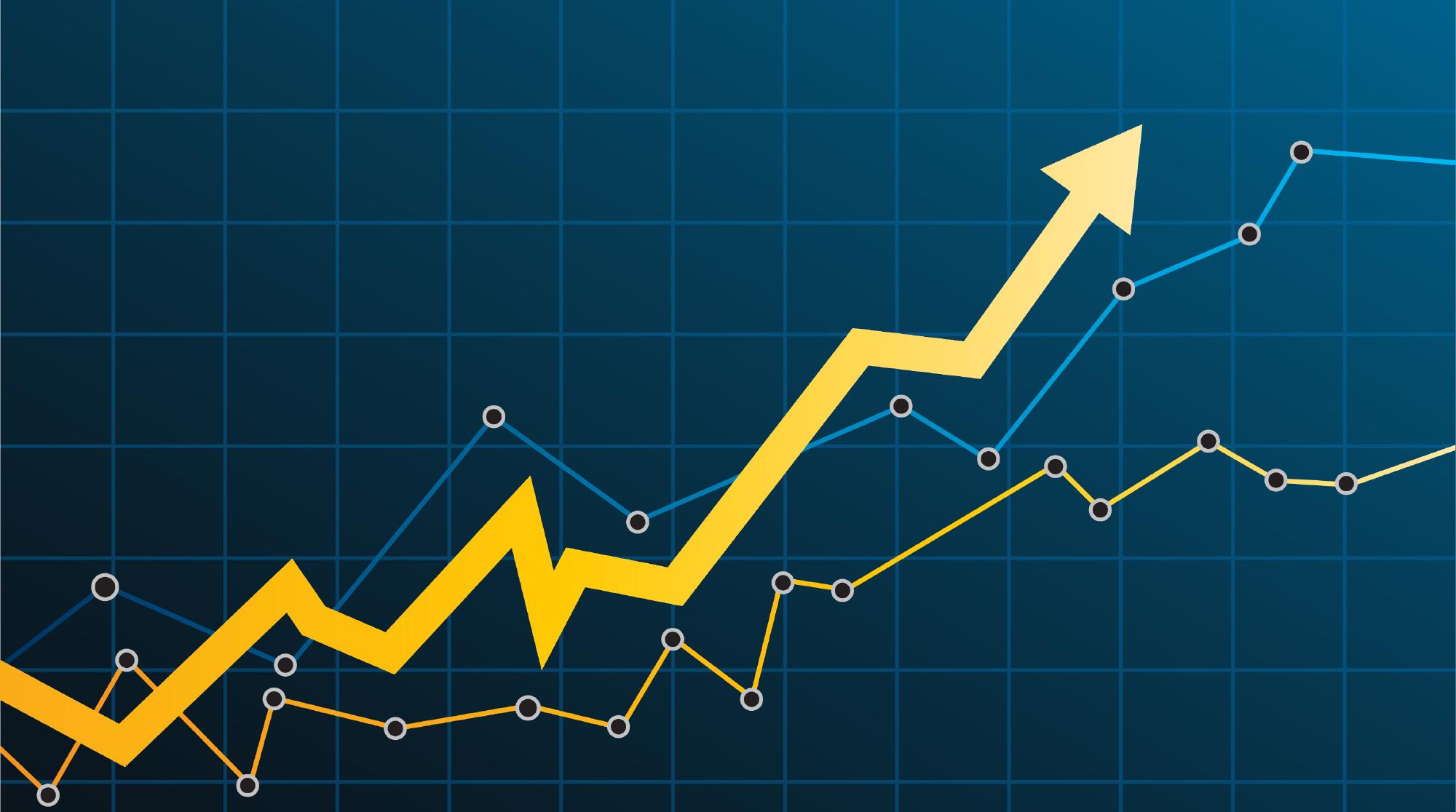
Author: Kerem Seçilmiş
There’s a popular saying that “what you don’t know can’t hurt you.” But this is not the case when it comes to supply chain costs. Many supply chain companies are not aware of the huge sums of money they are losing every day due to operational inefficiencies and manual planning processes. These flawed processes and practices lead to hidden, escalating costs that add up and take a tremendous toll on bottom lines.
In my role as Sales Director, I have the opportunity to speak with many prospective customers around the world and across various supply chain industries. Although each business is unique – as it faces its own supply chain challenges and possesses distinctive planning and operational capabilities – I see several common phenomena:
-
Most supply executives have a strong gut sense that they are losing something – operationally and financially – by using manual planning tools and techniques.
-
However, they don’t have the capability to examine their existing supply chain planning and operational processes to identify areas of inefficiency, and calculate and quantify exactly how much their companies are losing as a result of these ineffective processes.
-
They are not aware of exactly how much they could gain – in terms of decreasing costs and increasing productivity – by investing in an intelligent, integrated supply chain planning and optimization platform.
When we are engaging with potential customers, one of the first things we do is to run a full diagnostic assessment of their planning and operational processes, conduct a cost analysis to calculate how much they are losing by utilizing a manual planning system, and do an ROI analysis to demonstrate how much they stand to gain by implementing an automated supply chain planning and optimization system.
When we do this analysis and crunch the numbers, what we typically discover is that these supply chain companies are losing out – operational and financially – due to a number of factors including:
- Long planning cycles: It typically takes a medium-sized manufacturing company, for example, a minimum of two days to create a feasible production plan and many additional hours to update the plan in the wake of changing conditions in the market or on the shop floor. With an automated planning system, an optimal plan can be generated in a matter of minutes and revised on the fly.
Time is money in the supply chain world, and any time wasted due to manual planning activities, machine setup and production delays, or materials or workforce bottlenecks results in a spike in costs.
- Lack of planning accuracy and flexibility: If plans are created by human planners using manual methods and tools like Excel, they are prone to errors and unable to take into account the company’s complex supply chain constraints as well as its business KPIs, demand fluctuations, and production disruptions. This lack of planning accuracy and operational agility leads to a drop in on time, in full (OTIF) delivery performance – which in turn translates into unhappy customers and plunging revenues.
- Operational inefficiency: Generally speaking, relying on manually-generated plans results in subpar operational efficiency and customer satisfaction levels and skyrocketing costs associated with excess inventory, raw materials unavailability, employee overtime, resource utilization, etc.
So, in our initial interactions with potential customers, we usually try to analyze their existing planning and operational processes to pinpoint areas of inefficiency and sources of increased costs. Then we calculate how much they are losing due to these processes and estimate how much they stand to profit by implementing an intelligent planning and optimized decision making solution.
The results of our analysis and calculations are almost always a real eye opener for potential customers. And once we give them the hard numbers – and they are able to clearly see how much they are losing with their existing systems and processes and how much they could gain by utilizing an automated planning platform – it’s pretty much a no-brainer to invest in such a solution.
Just imagine how much you could save if you, for instance, increased your capacity utilization by 10%, decreased your inventory by 10%, or reduced your planning cycle time by 40% and the number of planners you employed by 50%. These are common results that our customers are able to achieve.
Many supply chain executives are reluctant to invest in supply chain planning and optimization platforms as they are concerned about the cost of these solutions – which, of course, are not cheap.
But a simple calculation of their current supply chain costs and the potential benefits of implementing an automated planning solution reveals that – even for the most expensive solutions in the market – ROI can usually be delivered in less than a year.
Once you have done the math and have the numbers in front of you, it’s an easy decision on whether or not to invest in an intelligent, integrated planning and optimized decision making solution.
If you would like to see ICRON in action, please contact us. If you have enjoyed this blog, you can find more content that you might enjoy here.