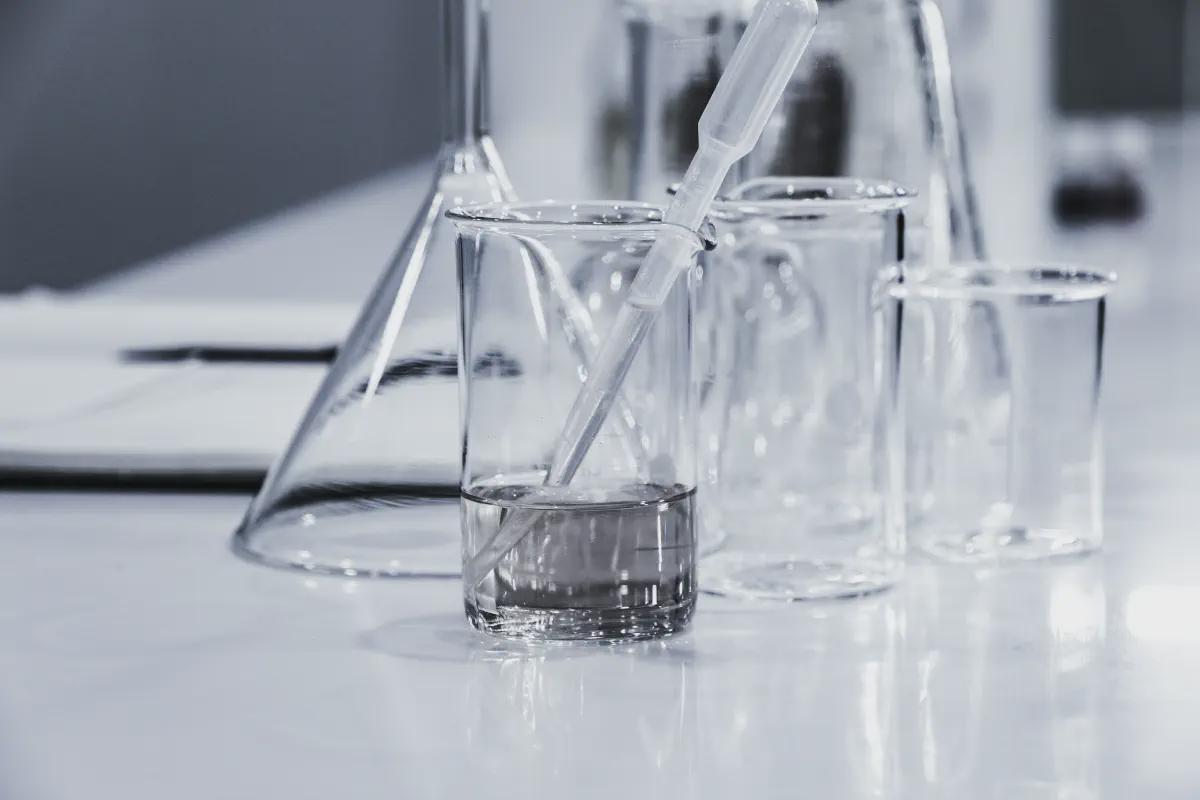
Author: Öykü Sorgun
The chemical industry is highly competitive. 96% of the products produced in the chemical industry require one or more chemical goods, and manufacturers in the chemical industry produce chemicals worth 4 billion dollars every year. In addition to the high demand, producing chemical products is not an easy process.
Due to the complexity, intricate problems can arise and each process from the procurement of raw materials to the production processes, needs to be done carefully. We had a conversation with ICRON’s Customer Service Manager Gamze Bilgi to discuss the challenges and current technological developments in the chemical industry.
Fluctuations in oil prices and unpredictable lead times
When the pharmaceutical industry is set aside, which is one of the sub-main breakdowns of the chemical industry, most products used in the chemical industry are derived from petroleum. One of the main factors affecting severely the oil industry is the fluctuations in oil prices. While the volatility in prices reflects negatively on the costs, it can cause a chain reaction that can cause the companies having difficulties in accessing raw materials and even going bankrupt.
Manufacturing firms usually tend to not hold inventory to reduce costs. However, they may be experiencing supply problems as products are supplied from long distance destinations such as the USA or the Far East and/or there is limited access to the location of the plant. In other words, raw material supply is one of the biggest problems in the chemical industry. In connection with this, supply times have become unpredictable due to the pandemic and the Ukraine-Russia war. For example, a product, expected to arrive within 45 days may arrive in 90. On top of that, this cannot be monitored properly, which makes forecasting from production to delivery is getting harder than it used to be.
Competence of manufacturers in digital supply chain tools needs to be increased
When all considered, we face a complex supply chain problem. In order to be able to do material planning, you need to know what the sales potential of the company is as well as what is the total supply capacity. To master what the market’s buying potential as well as the company’s supply capacity, a holistic demand, supply, capacity, and production planning approach is required which takes all aspects of the chemicals supply chain into consideration. change or disruption in this process affects the next stage or the whole chain. In order to manage this whole process in an optimum way, the competencies in digital supply chain tools need to be developed.
With today’s advanced AI/ML technologies, predictions of future demand and supply can be done more accurately. Accurate estimation involves analyzing large amounts of statistically retrospective data. In addition, the data to be analyzed must be stored somewhere. Depending on the forecasts, it is necessary to use tools that can make medium and long-term planning and provide different scenarios to decision makers. In this way, manufacturing companies in the chemical industry can control when and how much raw material they need and can make long-term contracts and determine their strategies accordingly. In addition, it helps companies to adapt to changing conditions while helping them identify which companies to connect with.
The assessment of digitalization
If we assess the state of digitalization, companies in the chemical industry are strong on the ERP side. They have mostly adapted ERP modules as they provide financial value. Adaptation of digital tools on the planning side is developing more slowly, especially compared to FMCG, and the automotive sector such as spare parts, tire, and supplier industry. Although the awareness of digital developments in the supply chain is increasing over time, the business follow-up of companies can remain at a daily level, and they may have difficulty in determining their future strategies through different scenarios. This causes production companies to not be able to adapt quickly to changing conditions and to lose time.
Some technologies need to be primarily adapted. S&OP can be used to align demand and supply in an optimal manner. While capacity planning can be done with procurement and optimized planning, it may be possible to improve the stock side with inventory planning. While ensuring all these developments, it is equally important that they work in integration with each other. Companies in the chemical industry can easily gain a competitive advantage with digital tools.
If you would like to see ICRON in action, please contact us. If you have enjoyed this blog, you can find more content that you might enjoy here.