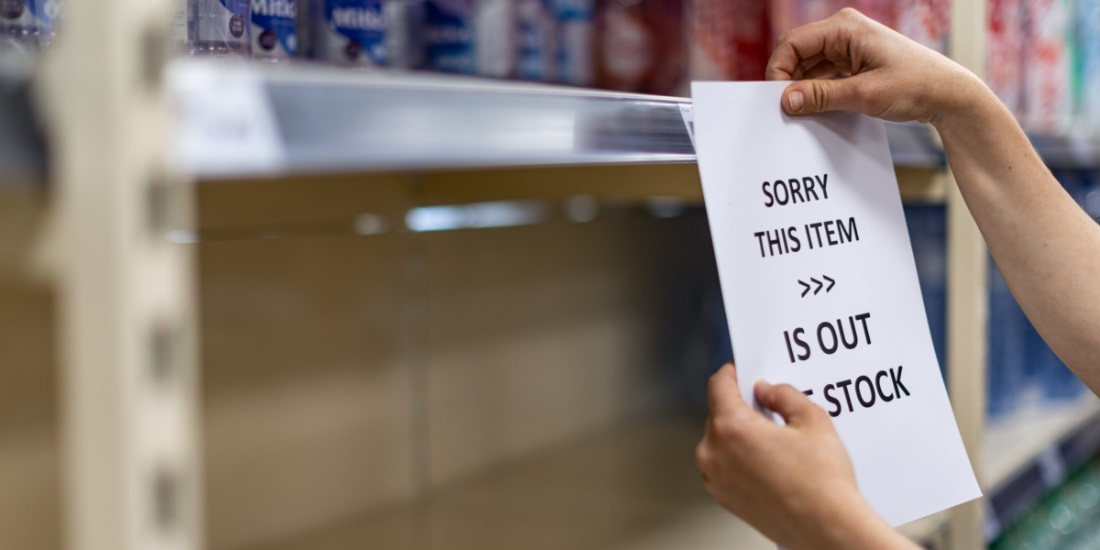
Recent research by APQS revealed that 87% of the organizations surveyed consider inventory planning the focus of their supply chain management for the next few years. This statistic still holds as supply chain disruptions continue to plague enterprise businesses.
Inventory planning is not just a task but a complex strategic imperative for any business. It is crucial for maintaining smooth operations, optimizing costs, and meeting customer demands. However, many companies struggle with common pitfalls that can disrupt this delicate balance. These include overstocking, stockouts, inaccurate forecasting, and inefficient supply chain management. Successfully navigating these challenges requires end-to-end visibility, optimization, data analytics, and cross-departmental collaboration.
This article outlines the common inventory planning pitfalls and offers practical, actionable insights to overcome them.
-
Avoiding Suboptimal Models in Inventory Planning:
In the dynamic world of supply chain management, the choice of inventory management models plays a pivotal role in driving operational efficiency and business success. However, many supply chain leaders end up selecting models that fail to account for all relevant variables, leading to inaccurate predictions and suboptimal decisions. Rather than settling for suboptimal models, it is essential for inventory managers to pursue a balance between usability and thorough analysis. By prioritizing advanced, data-driven inventory management models, supply chain leaders can transform their operations, minimize risks, and unlock new opportunities for growth and innovation.
-
Defining Clear Parameters for Efficient Inventory Management:
Defining the proper parameters for an inventory planning model provides transparency and determines the quality of the model's results. An ideal inventory planning model has no black boxes. It enables stakeholders to follow the inner workings of the model with ease. A transparent inventory planning model with precise functionality allows stakeholders to buy into the results.
-
Managing the Landslide Effect in Inventory Planning:
The ‘landslide effect’ refers to a drop in service levels when a company completes the peak season and enters a season of low demand. The landslide effect manifests because of high demand in the peak season that depletes the inventory, leaving little or nothing for the low-demand season. Everyone plans for the peak season and builds inventory for it. Still, most inventory managers forget to prepare for the transition period from peak to low season until it is too late. It is critical to consider the transition period when planning for inventory, identifying the landslide effect, and correcting the issue for the future.
-
Preventing Bias in Forecasting for Effective Inventory Planning:
Market complexities and uncertainties make it difficult to develop an accurate forecasting system for inventory planning. Some forecasts focus on point prediction or average value while disregarding market uncertainties. Others may introduce a systematic forecast bias, so they are always a bit off-target. A biased forecasting system can profoundly impact your inventory planning model, leading to incorrect stock safety levels. Continuously auditing the forecasting system and identifying areas for improvement can help keep an unbiased forecasting system for inventory planning.
There are various inherent challenges to managing inventory amidst supply chain disruptions. Besides the pitfalls mentioned above, numerous market volatilities, uncertainties, and constraints can hinder your efforts for efficient inventory management. The answer to navigating these pitfalls lies in advanced inventory management techniques. Some of them are listed below
- Multi-echelon Inventory Optimization (MEIO): MEIO solutions can suggest the correct inventory levels at each stage of the supply chain by optimizing inventory balance across multiple echelons and locations.
- Advanced Automation: Artificial intelligence-enabled tools automate analytical tasks like identifying root causes, sending alerts, or augmenting decision-making based on findings.
- Optimized Safety Stock Calculation: Move beyond traditional inventory target calculations and use machine learning to determine the optimal safety stock and to define the recommended actions and alerts.
- Enhanced Analytical Ability: Incorporate cost-to-serve analysis and broader data insights to enhance analytical abilities of your inventory management system.
- End-to-End Visibility: Implementing end-to-end visibility can ensure real-time monitoring, streamline operations, and enables proactive responses to disruptions to reduce inefficiencies.
- Risk Mitigation: Advanced techniques prioritize risk mitigation by identifying potential supply chain vulnerabilities and enabling preemptive actions. These strategies reduce the likelihood of stockouts, overstocking, and other costly disruptions, safeguarding business continuity.
Successful inventory planning hinges on recognizing and addressing common pitfalls with strategic, data-driven approaches. A blend of strategic foresight, robust data analytics, and adaptability to market dynamics can elevate business inventory planning. By focusing on these core elements, businesses can navigate complexities and turn potential pitfalls into opportunities for growth and innovation. The journey is challenging, but with the right approach, it becomes a vital component of a thriving, resilient supply chain.