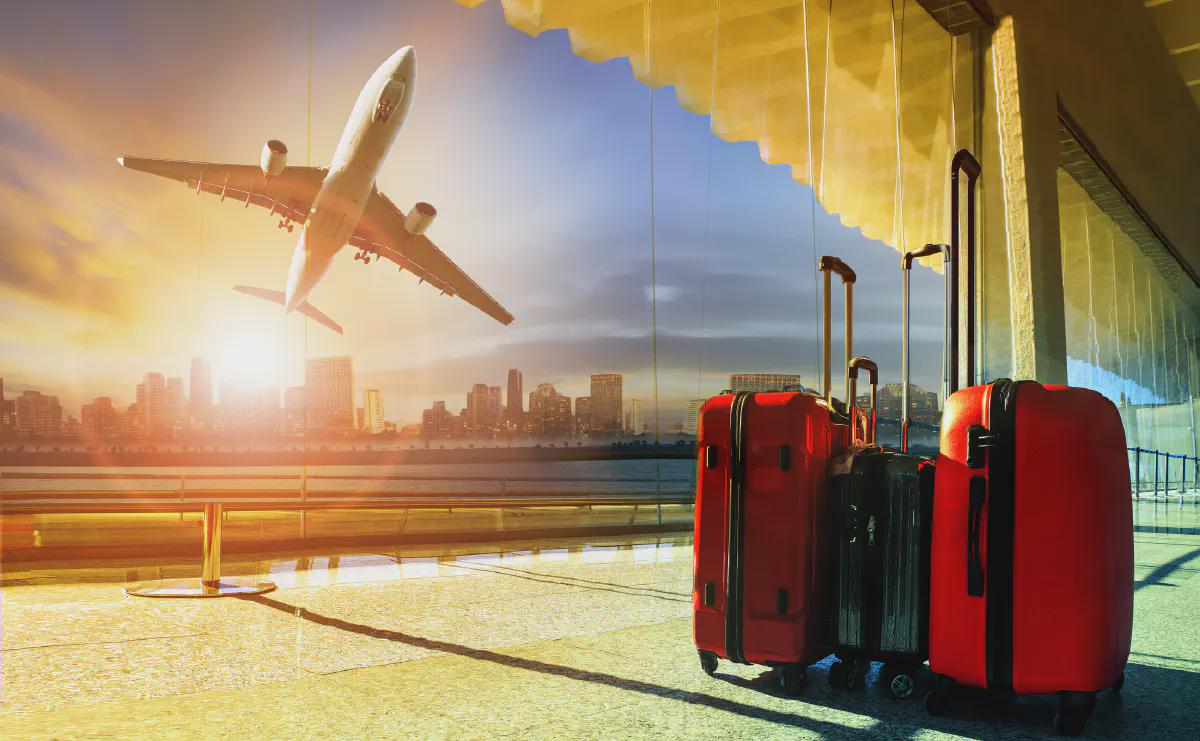
Author: Mine Kaçan
In Turkey, where I’m based, we are about to enter the summer holiday season – when workers across industries press the pause button and take a (well-deserved) break from their normal, professional operations. For most workers, the holidays are a time of rest and relaxation. But, for planners and other key decision makers in the manufacturing industry, holidays can be a time of high stress.
This stress stems from the simple fact that during the holidays, most employees want to take a vacation and (understandably) don’t want to work! Operating with a dramatically reduced workforce capacity (sometimes decreased by more than 90%), manufacturing firms often struggle to ensure that production operations continue to run smoothly during the holiday periods so that they can meet their KPIs such as maximizing on time, in full (OTIF) performance and customer satisfaction and minimizing costs.
Besides diminished workforce capacity, there are also other constraints such as materials availability – as many suppliers will slow down or suspend their operations during the holidays as well – that make the manufacturing process particularly challenging during this period of time.
The key to keeping manufacturing operations running seamlessly and successfully during the holidays is planning. Unfortunately (due to the complexity of manufacturing operations, which usually involve numerous products, processes, machines, workers, and component parts) manual planning techniques and tools are not up to the task.
An integrated, automated supply chain planning and optimization solution, like ICRON, can enable manufacturing companies to optimally plan for the holidays, so that operations keep rolling along even though most of the planning, production, and other departments are away from the factory and in vacation mode.
With an algorithm-based supply chain planning and optimization platform, manufacturing companies can optimize their holiday planning and operations by conducting:
Capacity planning
To properly prepare for the holiday periods, manufacturers must be able to plan their capacity months ahead of time. Once planners know their customer orders, inventory levels, and demand forecasts, they can automatically generate optimal weekly capacity plans and determine their material requirements, shift assignments, and machine schedules. This enables manufacturers to prepare well ahead of time so that they can optimize their capacity utilization during the holiday season.
With an algorithmic capacity planning solution, manufacturing companies can achieve complete, mid-term visibility and control over their supply chain and can figure out which particular machines, materials, and workers they need to satisfy demand (in the most efficient manner possible) before, during, and after the holidays. Planners can also conduct “what-if” analysis weeks or even months ahead of the holidays, to evaluate various scenarios based on their KPIs – so that they can make the best decisions about which machines and workers they should deploy during the holiday season.
Production scheduling
With an algorithmic, automated supply chain planning and optimization solution, planners can create detailed daily production schedules – that optimize their resource utilization, maximize productivity, and OTIF performance, and minimize costs – before the holidays begin, and share these with the production and other departments. Then, when the holiday period actually starts (and there are most likely no planners working), the planning system runs on auto-pilot on a daily basis (like it normally does), monitors conditions on the shopfloor in real-time, and keeps manufacturing operations humming along.
Real-time dispatching
Sudden disruptions in production – due to, for example, machine breakdowns or the unexpected unavailability of raw materials – can occur at any time and can be a major source of stress during the holidays for manufacturing companies. Best-of-breed algorithm-based supply chain planning and optimization solutions like ICRON, however, possess a functionality called “real-time dispatching” – which enables manufacturing companies to efficiently and effectively respond to disruptions on the production process.
With this real-time dispatching capability, data on the disruptions will be instantly fed from the shopfloor directly into the planning system, which will automatically, optimally revise the daily production plans, and communicate this revised plan to stakeholders throughout the organization. This eliminates the need for a planner to be “on call” during the holidays.
If you would like to see ICRON in action, please contact us. If you have enjoyed this blog, you can find more content that you might enjoy here.