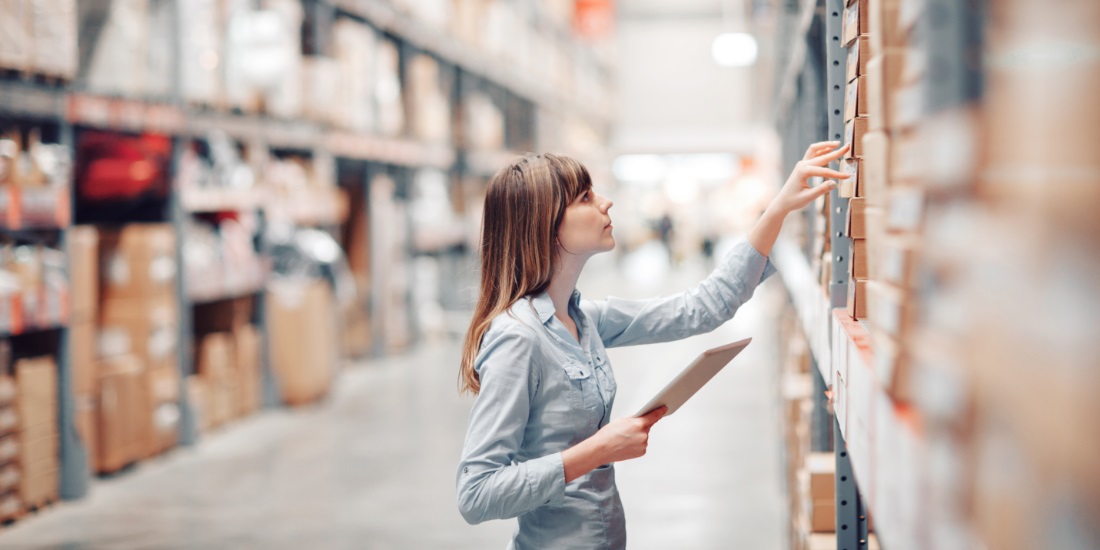
Order management is the backbone of modern supply chain planning, ensuring products move efficiently from manufacturers to end customers. The order management process encompasses every step from order creation to delivery, including tracking, handling, and fulfilling customer orders. In a world increasingly reliant on e-commerce and rapid fulfillment, effective order management is pivotal to maintaining customer satisfaction and operational efficiency.
A well-structured order management system enhances visibility across the supply chain, optimizes inventory levels, and reduces costs. It is a critical link connecting demand, procurement, inventory, and distribution, helping organizations adapt swiftly to changing market conditions. In today’s competitive landscape, companies that master order management can differentiate themselves through faster response times, reduced errors, and superior customer experiences, reinforcing their position as industry leaders.
One of the primary benefits of order management systems is the visibility they provide across the entire supply chain. Real-time data on inventory, order status, and delivery timelines helps companies quickly adapt to changing market conditions, mitigate risks, and improve decision-making processes. For example, businesses can identify potential disruptions, track the progress of shipments, and adjust inventory levels based on current demand, all of which are essential for minimizing lead times and enhancing service levels. This level of visibility is critical for operational efficiency and for fostering trust and reliability with customers by providing accurate and timely updates regarding their orders.
In today’s competitive landscape, the ability to manage orders effectively sets industry leaders apart. Companies that excel in order management in supply chain operations differentiate themselves through faster response times, lower error rates, and superior customer service. By adopting a comprehensive and streamlined order management system, businesses can significantly reduce operational costs, improve workflow efficiency, and provide a more seamless customer experience. This, in turn, helps companies maintain a competitive advantage and build long-term customer loyalty by consistently delivering on promises.
Understanding the Fundamentals of Order Management
-
Definition and Key Objectives of Order Management
Order management in supply chain is a crucial process encompassing the end-to-end tracking, processing, and fulfillment of customer orders. It involves managing the flow of products from inventory to customers, ensuring accuracy, efficiency, and customer satisfaction. The primary goals of OM are to streamline order fulfillment, minimize lead times, reduce errors, and enhance visibility across the supply chain. Effective order management ensures that customers receive the right products at the right time and in optimal condition, ultimately improving service levels and fostering trust. It plays a central role in aligning inventory with demand and optimizing operational efficiency.
-
Why Order Management is Crucial for Supply Chain Efficiency
Order management is crucial in optimizing supply chain operations, reducing costs, and ensuring customer satisfaction. Businesses can minimize manual errors, improve inventory accuracy, and enhance workflow efficiency by automating and streamlining order processes. Effective order management reduces lead times, optimizes warehouse operations, and prevents stockouts or overstock situations, ultimately lowering operational costs. Moreover, order tracking systems enhance visibility and improve communication and responsiveness, increasing customer satisfaction. By integrating order management with overall business objectives, companies create a seamless flow from order capture to fulfillment, fostering a more resilient and efficient supply chain.
The Order Management Process
-
Optimizing Order Creation and Entry for Accurate Fulfillment
Order creation and entry is the first step in the order management process. It involves placing and capturing customer orders through multiple sales channels, such as online platforms, mobile apps, and in-store purchases. Ensuring accuracy during this stage is crucial, as errors can lead to fulfillment issues and customer dissatisfaction.
-
Streamlining Order Processing and Verification Steps
Once an order is captured, it undergoes processing and verification. This stage includes validating order details, checking inventory availability, and verifying payment information. Adequate verification ensures that orders can be fulfilled without delays and prevents stockouts or incorrect billing issues.
-
Ensuring Efficient Order Fulfillment and Delivery
The next stage is order fulfillment and delivery, which involves preparing, picking, packing, and shipping products to customers. Efficient order fulfillment strategies ensure that products are dispatched promptly, leading to on-time deliveries and customer satisfaction.
-
Enhancing Post-Fulfillment Activities for Customer Satisfaction
Post-fulfillment activities encompass handling returns, customer service, and feedback loops. This step is essential for managing customer expectations, addressing issues after delivery, and gathering valuable insights to improve future processes. Businesses can enhance customer loyalty and continuously refine their operations by effectively managing returns and feedback.
Critical Components of an Effective Order Management System (OMS)
-
Maximizing Integration and Automation for Order Management Efficiency
Integration with other supply chain systems is vital for driving automation and accuracy in order management. By connecting OMS with systems like inventory, procurement, and shipping, businesses can streamline data flow, eliminate manual processes, and reduce errors. Automation ensures that orders are processed swiftly and accurately, improving overall efficiency.
-
Enhancing Inventory Visibility and Control in Order Management
An effective OMS provides real-time inventory visibility and control, ensuring accurate stock levels and optimal inventory placement. This visibility helps businesses avoid costly issues like stockouts or overstock situations, enabling them to meet customer demand more efficiently while minimizing holding costs.
-
Leveraging Order Tracking and Real-Time Data for Visibility
Order tracking and real-time data capabilities provide transparency throughout the order lifecycle. Customers and stakeholders benefit from real-time updates, which enhance communication and help manage expectations. Businesses can ensure higher customer satisfaction and loyalty by enabling proactive responses to potential delays or issues.
Challenges Faced in Supply Chain Order Management
Every business faces different challenges of order management in supply chain planning. The exact aspect of supply chain planning impacted by unpredictable factors depends on the industry, economic circumstances, and global business dynamics. However, below is a look at the most common challenges in supply chain order management.
-
Overcoming Data and System Integration Challenges in Order Management
Legacy systems and the lack of synchronization between different data sources are significant challenges in order management. Disconnected systems lead to inefficiencies, data discrepancies, and manual errors, making it difficult for businesses to achieve seamless operations and accurate decision-making.
-
Reducing Order Errors and Fulfillment Delays for Better Efficiency
Errors during order entry or processing and fulfillment delays can severely impact supply chain performance. Inaccurate orders or delays can result in dissatisfied customers, increased return rates, and lost sales opportunities, ultimately affecting a company’s reputation and profitability.
-
Effectively Managing Customer Expectations in Order Management
Managing customer expectations has become increasingly challenging with growing demands for faster delivery and order accuracy. Customers expect timely deliveries, complete transparency, and flexibility, which can be difficult without robust order management processes and systems.
Benefits of Order Management Systems in Supply Chain
Streamlining order management brings numerous benefits that enhance overall supply chain efficiency. By adopting an optimized order management system, businesses can achieve significant cost reduction, boost customer satisfaction, and improve inventory management. The benefits of order management system integration are crucial for maintaining competitive advantage in today’s dynamic market. Below, we explore the key advantages of streamlined order management and how they contribute to effective supply chain performance.
-
Achieving Cost Reduction and Efficiency Through Order Management
Streamlined order management processes reduce operational costs by minimizing manual interventions, enhancing inventory accuracy, and optimizing order fulfillment. Efficient workflows lead to faster order processing, reduced labor costs, and minimized errors, contributing to significant savings.
-
Boosting Customer Satisfaction and Retention with Order Management
Accurate and timely order deliveries are critical for customer satisfaction and loyalty. A streamlined order management process enables businesses to consistently meet customer expectations, fostering positive experiences that drive customer retention and repeat business.
-
Optimizing Inventory Management with Streamlined Order Processes
Streamlined order management helps businesses prevent stockouts or overstock situations by optimizing inventory levels and balancing supply with demand. Improved inventory management ensures that products are available when customers need them, minimizing excess stock and associated carrying costs.
Best Practices for Optimizing Order Management
-
Utilizing Advanced Order Management Software
Leveraging advanced OMS solutions can significantly enhance order accuracy, speed, and visibility. These systems automate routine tasks, provide real-time updates, and help manage orders more efficiently, allowing businesses to focus on strategic improvements and customer satisfaction.
-
Fostering Cross-Departmental Collaboration in Order Management
Effective order management solutions facilitate collaboration across multiple departments, including sales, logistics, and customer service. Encouraging better communication and alignment among these teams ensures that all stakeholders are informed and can contribute to a seamless order management process.
-
Implementing Regular Audits for Continuous Order Management Improvement
Regular audits of order management processes help identify inefficiencies and areas for improvement. By continuously refining processes to keep up with changing market needs, businesses can ensure their order management practices remain competitive and effective.
Future Trends in Order Management for Supply Chain Planning
-
Artificial Intelligence and Machine Learning
AI and ML transform order management by enabling predictive analytics for demand forecasting and more intelligent decision-making in order fulfillment. These technologies help optimize inventory, reduce lead times, and improve the overall efficiency of supply chain operations.
-
Omnichannel Order Management
As customers increasingly shop across multiple channels, an omnichannel approach to order management has become essential. Businesses must ensure a seamless experience across all sales channels, providing consistent inventory visibility and order fulfillment regardless of how or where customers choose to shop.
-
IoT and Real-Time Order Tracking
The Internet of Things (IoT) is playing a growing role in providing real-time updates and enhancing transparency in order management. By using IoT devices to track shipments and monitor inventory, businesses can improve operational visibility, reduce delays, and increase customer satisfaction.
A well-optimized order management system forms the core of a resilient supply chain, ensuring efficient flow of goods, minimizing disruptions, and improving overall performance. If you’re looking for how to improve order management in supply chain operations, it’s crucial to focus on addressing integration challenges, leveraging advanced technologies, and continuously refining processes. By addressing common challenges, adopting best practices, and preparing for future trends, businesses can enhance operational efficiency, reduce costs, and provide superior customer experiences.